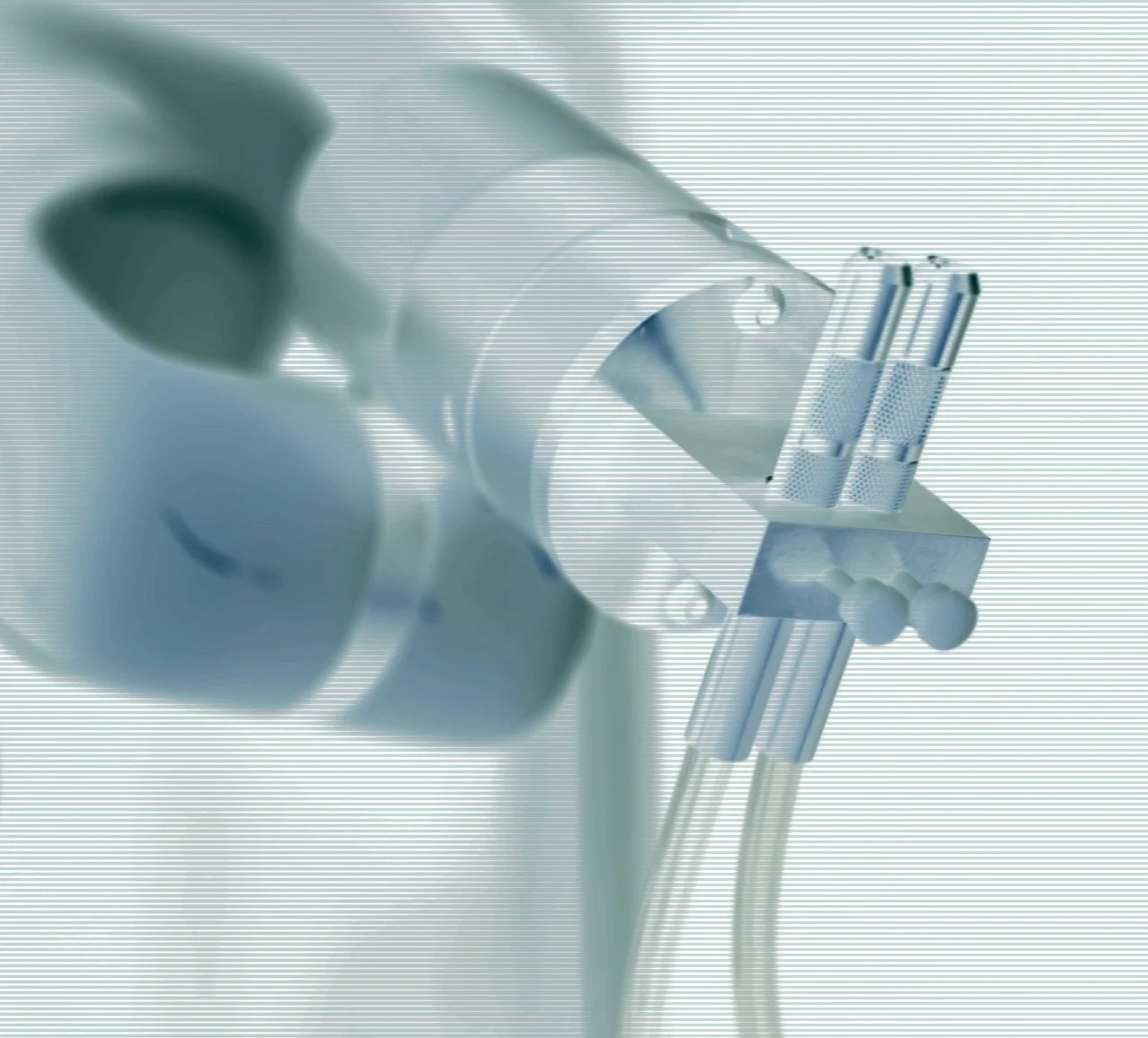
Meet xFAB: Himed’s Newest Fully Automated Blasting System
Discover how Himed’s newest in-house innovation, xFAB, enhances the precision, repeatability, and responsiveness of implant surface treatments across both R&D and production workflows. Built entirely by our engineering team, this fully automated system reflects our commitment to controlled, scalable, and regulation-ready processes.
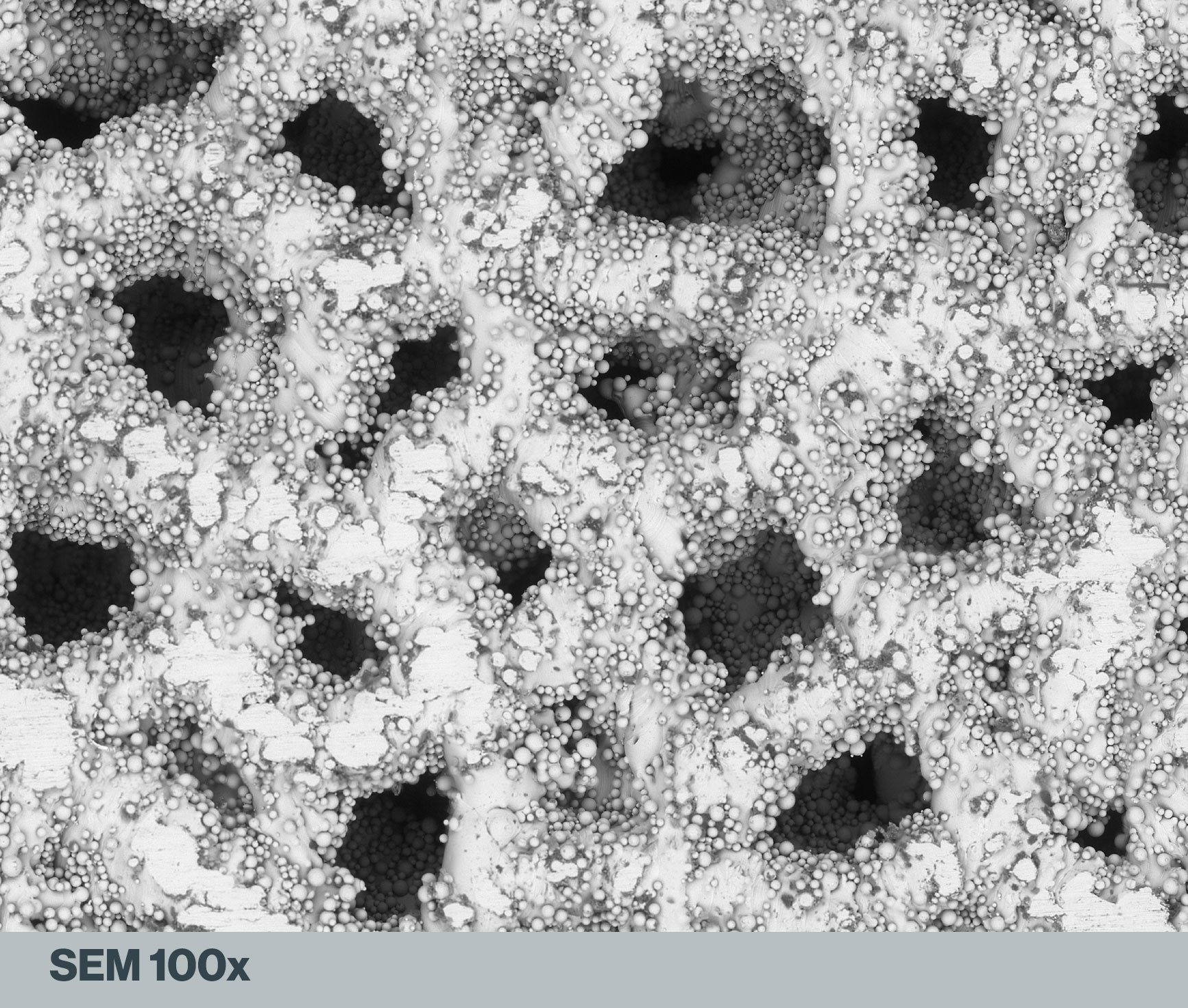
Al2O3, Glass Beads, and Apatitic Abrasive: Comparing Post-Processing Options for 3D-Printed Titanium Medical Implants
For the best chance of successful osseointegration, titanium and titanium-alloy implants need to undergo a surface finishing process. Research has shown that specifically textured surfaces on Ti implants can increase bone-to-implant contact and encourage new tissue growth around the device.
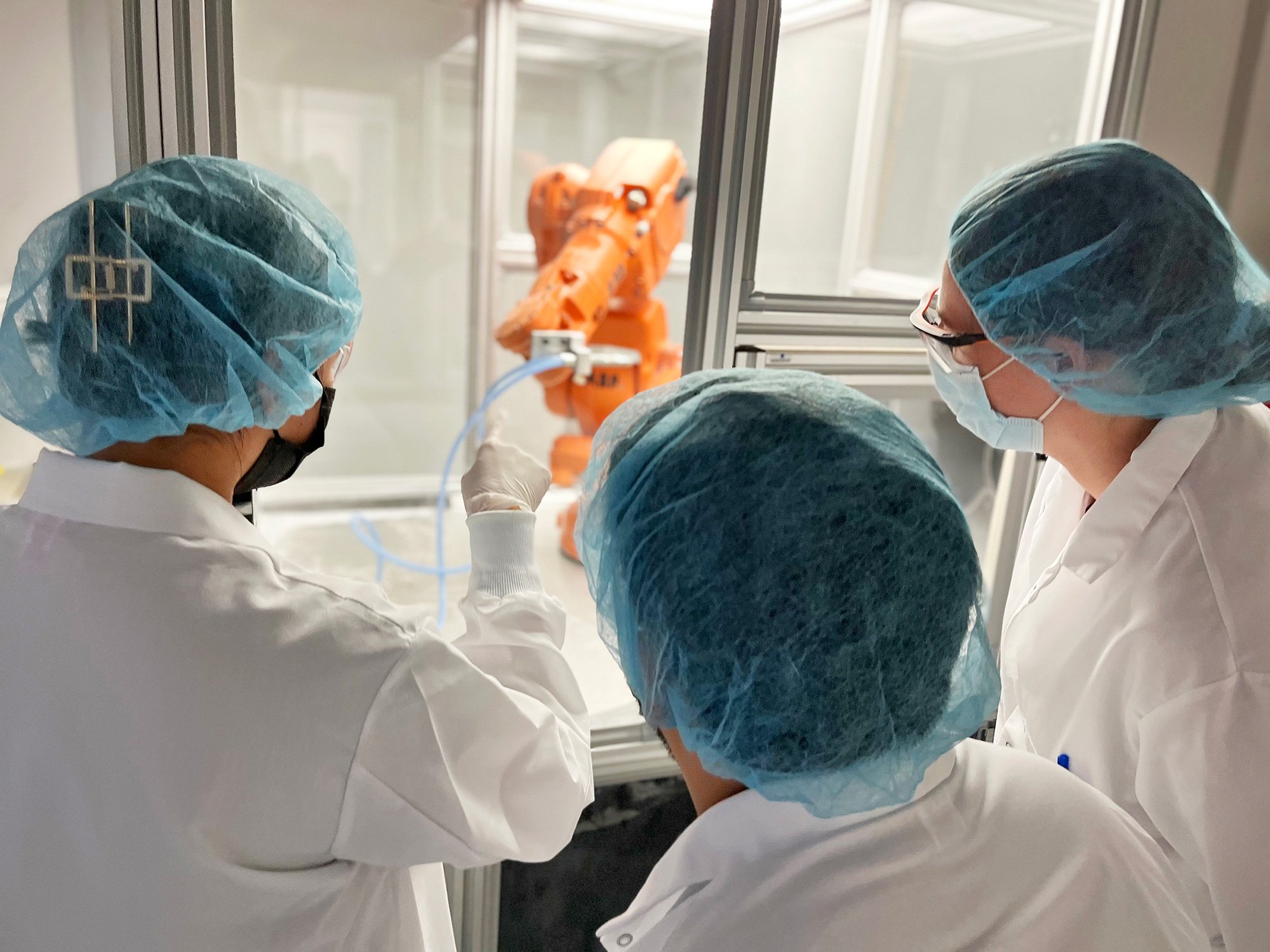
Himed’s MCD Apatitic Abrasive Blasting Capacity Is Growing
Here at Himed, we just added a new member to our team of robots. We call it iFAB (short for “fully automated blaster”). It’s a highly-dexterous, automated industrial robot with six-axes of motion, that is contained within a new production cell. The iFab has been specifically designed to deliver our biocompatible MATRIX MCD® treatment to medical devices, dental implants, and orthopedic implants.
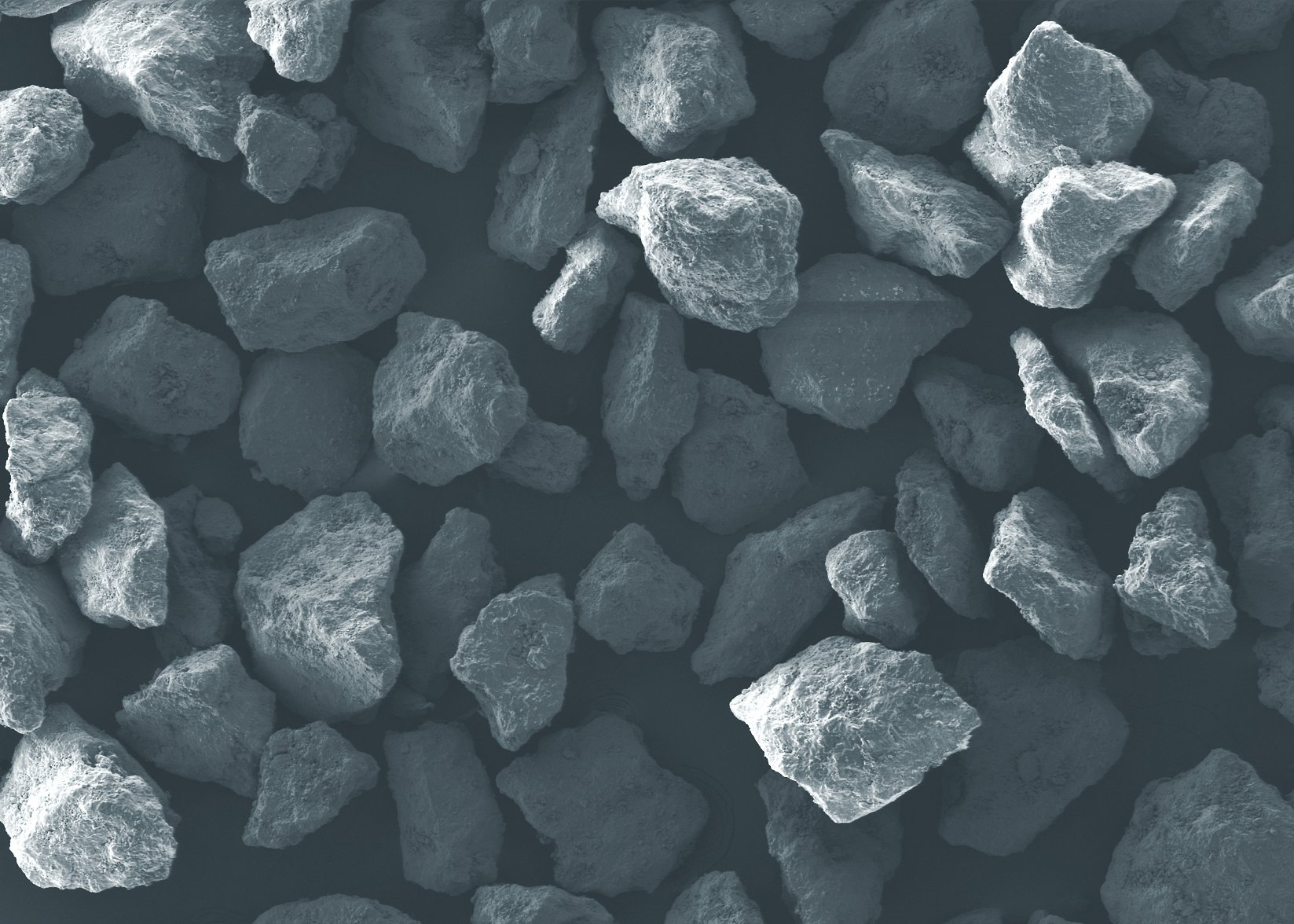
An Ideal Post-Processing Solution for Additive-Manufactured Medical Devices
Few things have been as potentially revolutionary for the medical device industry as 3D printing. The process allows implant manufacturers to design and produce innovative products quickly and efficiently. But additive manufacturing does introduce a few specific issues medical implant designers and fabricators must take into account.
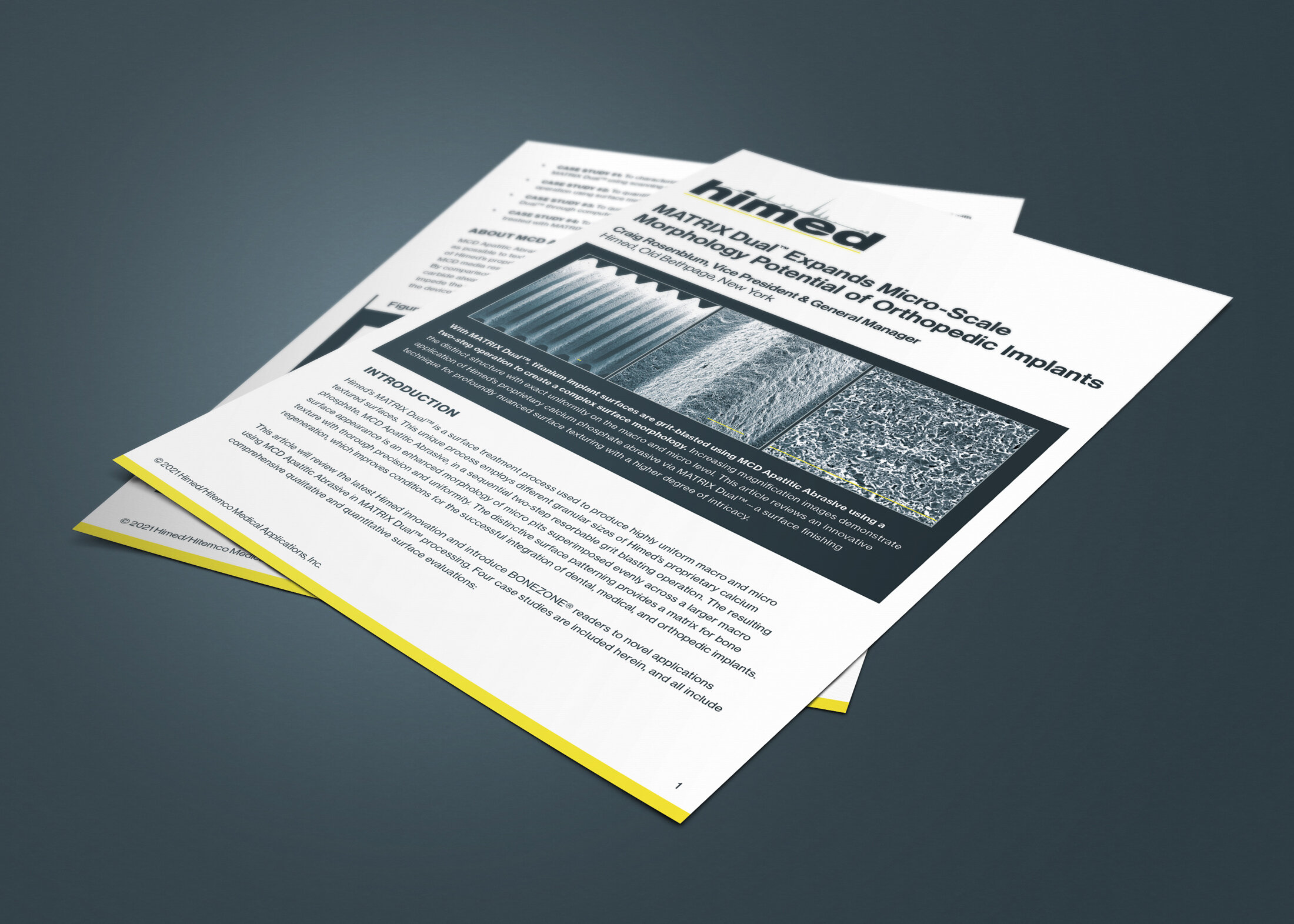
Himed Announces New MATRIX Dual® White Paper Publication
As the medical industry continues to explore the conditions for successful implant integration with the human body, closer attention is being paid to the surface morphology of a given device. That “closer attention” is taken quite literally in our latest white paper. In it, four case studies are reviewed that use advanced scanning technology to characterize—at the submicron and nanoscale level—surfaces treated with our two-step MATRIX Dual® process.